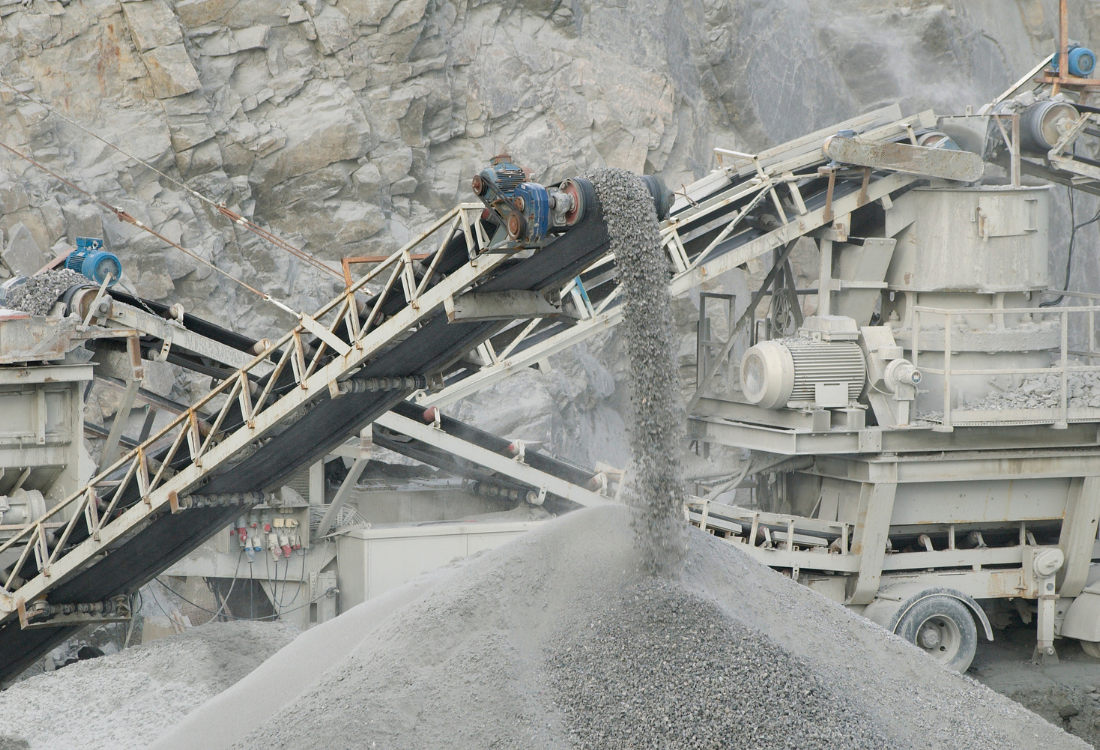
Benefits Of Chemical Foam Dust Suppression Systems For Dust Control In Quarries
Quarrying and extraction operations are notorious for generating large volumes of dust, arising from the handling and extraction of various aggregates and minerals. Airborne dust particulates arising from crushing and screening, material transfers, loading and unloading, storage areas, and even vehicles and mobile plant moving around site, pose a significant threat to worker safety, and can also cause an environmental hazard if dust spreads to the surrounding area. Chemical foam suppression systems are a cost-effective and efficient means of controlling dust in various parts of the quarry, and can be tailored to the needs of individual operations.
Read on to find out about the main benefits:

Reduced Water Consumption
The traditional means of controlling emissions in high dust environments is by sprinkling with water to reduce the dusts’ volubility and prevent particles from becoming airborne. However, in busy quarrying and crushing operations this can consume vast quantities of water, as well as having unwanted side-effects such as material saturation, increased corrosion on equipment, and problems arising from run-off. A chemical foam system significantly reduces your water usage by creating a foam matrix or barrier that binds with the dust particles, effectively suppressing them with a fraction of the water needed by a conventional sprinkler. During aggregate crushing, for example, a foam application can cover high risk dust areas without overloading your conveyor belts or silt producing equipment. Fixed foam systems are also useful in quarries with limited or variable access to water, and at sites where water management systems are costly to maintain.
Versatility For Complex Extraction Operations
Many quarries operate across diverse terrains, and extract materials ranging from coarse aggregates to fine sands. Dust sources vary, therefore, and require an adaptable solution for effective suppression. Chemical foam systems give you this versatility to match your formulation to specific operational requirements. Where large volumes of fine dust particles are created, such as at primary crushers, a foam with high binding properties can be used, while a lighter foam may be sufficient to suppress dust during stockpile loading and conveyor transfers. We can work with you to integrate the appropriate system and suppression agent into your extraction processes, addressing the challenges of variable dust risks without disrupting your workflows or requiring extensive retrofitting to your plant.
Better Air Quality Around Crushing and Screening Sites
Dust emissions in quarries are often highest around the crushers, where hard rocks are broken into finer aggregates. These are the areas most prone to airborne particles that can jeopardise human health and impact local air quality. A fixed chemical foam suppression system in these dust prone areas can help to create a long-lasting barrier over your primary dust sources, minimising particle migration and avoiding fine dust from becoming suspended in the air. This can improve on site health and safety by reducing exposure to harmful dust – such as respirable crystalline silica.
Quarry Foam Suppression Systems From Best Chem: Find Out More
Our range of innovative foam suppression measures and equipment are effective dust control solutions for a wide range of quarrying and extraction applications. Find out more by clicking here, or contact one of our experienced team directly to request a call back.

Image Source: Canva