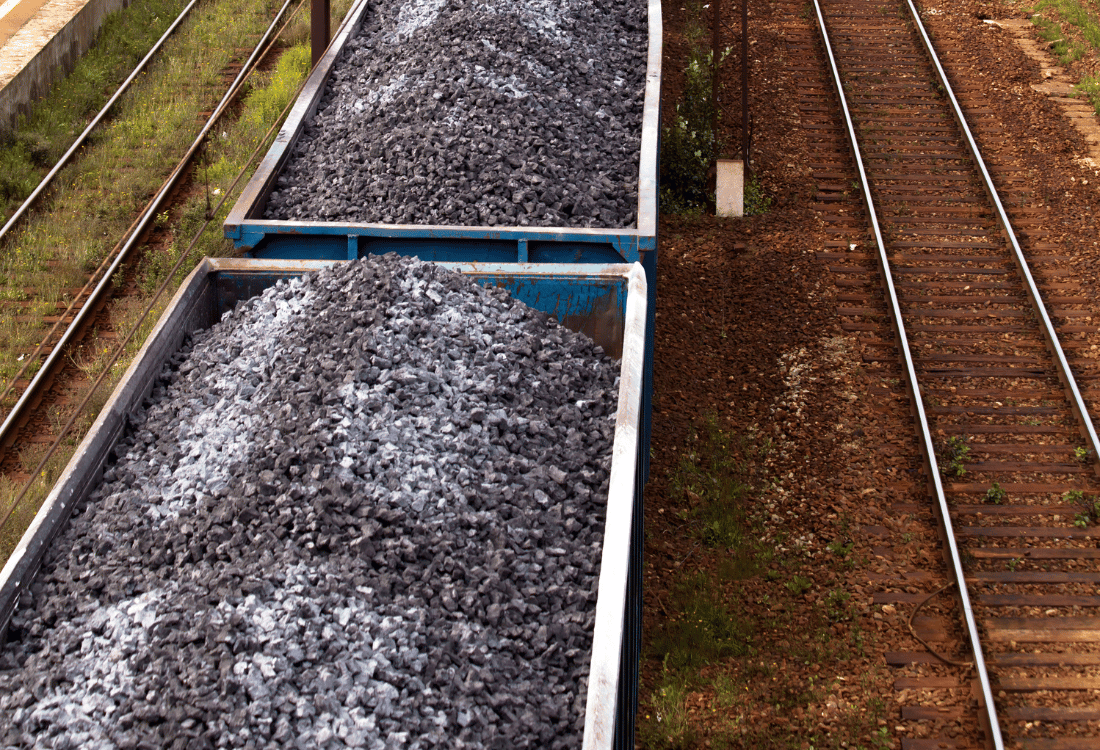
Methods Of Rail Wagon Encapsulation To Prevent Dust Lift Off In Transit
Dust lift off is a significant health and safety hazard when transporting many categories of bulk materials by rail. Without effective dust control measures or rail wagon encapsulation solutions in place, material handling before and during transit can lead to fugitive dust emissions, posing severe health, operational, and environmental challenges. There are a variety of strategies that operators can adopt to prevent dust lift off in transit.
In this article, we will examine 3 methods of dust suppression and the effect of chemcial sealments, looking at their advantages and disadvantages.

3 Methods Of Dust Suppression
1. Covered Rail Wagons
One of the most straightforward ways to reduce dust emissions from rail wagons is to cover them over in transit! This is a safe and effective strategy but can involve significant capital outlay. Applying sheets manually to wagons containing hazardous materials can also be labour-intensive, time-consuming, and pose a safety risk to workers. A covered rail wagon provides a physical barrier that shelters the material from direct exposure to wind, rain, vibrations, and other environmental factors that cause lift off. Covered wagons are especially effective for transporting fine, light, or dry materials that are prone to becoming airborne. Covers can be either fixed or detachable, depending on the design.
2. Mechanical Retractable Systems
A development of the covered rail wagon idea is the mechanical retractable system, which integrates a flexible cover onto the rolling stock that can automatically extend and retract over the load. This strategy allows rapid encapsulation of bulk materials after loading, with minimal dust escape during operation. The retractable design also facilitates efficient unloading, making the system operationally practical for operations that require frequent material transfers. However, while improving efficiency, safety, and coverage, mechanical retractable systems require robust installation, regular maintenance, and often retrofitting onto existing rolling stock. Initial costs can, therefore, be high, and installation can be complex.
3. Pre-wet The Material To Increase Moisture Content
Bulk material with a higher moisture content is heavier and less likely to become airborne while on the move. Therefore, pre-wetting the load to help bind dust particles together is a potent stockpile dust control measure as well as a strategy for preventing dust lift off in transit. The strategy involves spraying the stockpiled material with water or a foam dust suppression agent so that the moisture content is evenly distributed. This works especially well with coal, clinker, construction aggregates, and other granular or powdery substances. However, there are some cons. For instance, increased moisture can lead to ‘bridging’ in the wagon, causing uneven load distribution and reducing capacity, and material sticking inside the wagon’s surface can cause difficulty during unloading. There is also the extra weight to consider. An extra 1 to 2% extra weight from transporting water can be costly and reduces your capacity for transporting product.
Chemical Sealants or ‘Veneers’
Chemical sealants create a crust that seals the exposed material in the wagon. This is a safe and proven process that can be automated, and doesn’t require any structural changes to your rolling stock. Veneers are directly sprayed onto the load’s surface, establishing a durable layer that is resistant to wind currents and transit disturbances. These are straightforward and cost-effective encapsulation solution for longer transit routes, or when transporting materials in windy weather.
Find Out More About Rail Wagon Encapsulation
At Best Chem, we offer a variety of specialist dust suppression solutions tailored to the needs of your product and application. To find out more, please contact one of our team today by clicking here.

Image Source: Canva