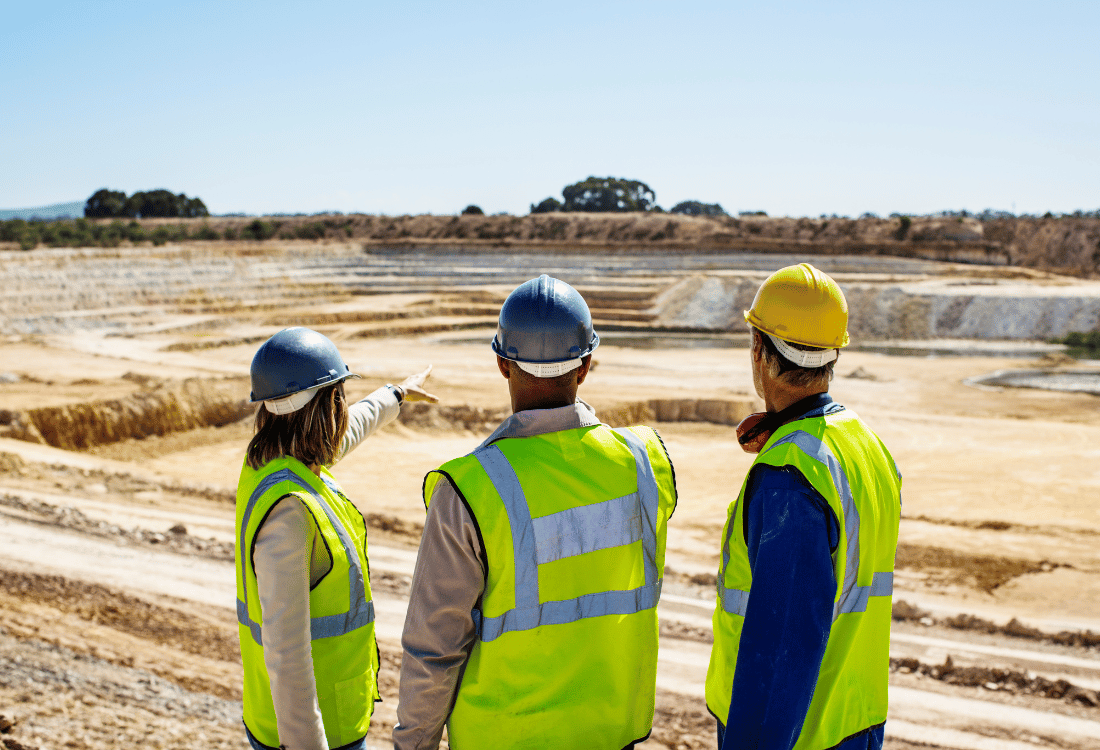
Dust Control Systems: Why Quarrying Operations Need To Limit Silica Exposure
Silica is one of the most dangerous components to take into your lungs, which is why ‘sandblasting’ is illegal in the UK and many other jurisdictions. Unfortunately, quarries contain abundant sources of silica, trapped within limestone, gravel, sand, and other stones, and released into the air through drilling, cutting, and crushing.
It’s essential for quarry workers to be aware of the many health risks associated with silica exposure (which include silicosis, lung cancer, and rheumatoid arthritis) and to wear the appropriate PPE at all times. However, even with the best PPE, silica dust still sticks to plant, machinery, and clothing, making exposure difficult to completely rule out risk.
For this reason, limiting silica exposure in a quarrying operation goes beyond worker training and PPE. To minimise risk, silica dust should be addressed at the source through a dust suppression system. Doing so can contribute to a healthier work environment, avoid potential health issues among your workers and reduce environmental harm.

Dust Control Technology For Quarries
There are a variety of dust control strategies available to quarries, depending on the materials you are working with, and your site’s level of risk. Two such solutions are: atomised misting and foam dust suppression systems.
An atomised misting system ejects a low-density water vapour or fog to capture and suppress air-borne dust particles. This reduces the risk of workers inhaling silica dust at critical areas of the site, such as vehicle loading/offloading areas, storage bays, and hoppers. Misting systems can also assist with humidification, cooling, and odour control, adding more value to your project.
Foam Dust Suppression is an alternative dust control technology, which produces a low-moisture foam spray to capture and suppress fine dust particles. The foam solution has enhanced wetting properties and a greater surface area, making it more effective than a plain water-based system. Foam Systems also dampen the dust particles before they become airborne, ensuring they stay with the material instead of settling nearby and drying out. This is a safer solution in high-risk quarries and also reduces water usage and environmental footprint.
Of course, many operations use a combination of both misting and foam control systems, with foam used to treat material during processing and a misting system used to capture stray particles during tipping/loading.
Find Out More
Best-Chem are one of Europe’s leading manufacturers of foam dust suppression systems and specialist foaming agents, with over 100 installations worldwide and 20 years of experience serving customers in the mining, quarrying, power generation, and industrial processing industries. To discover how we can support your operation, please contact one of our knowledgeable team today by clicking here.
Image Source: Canva