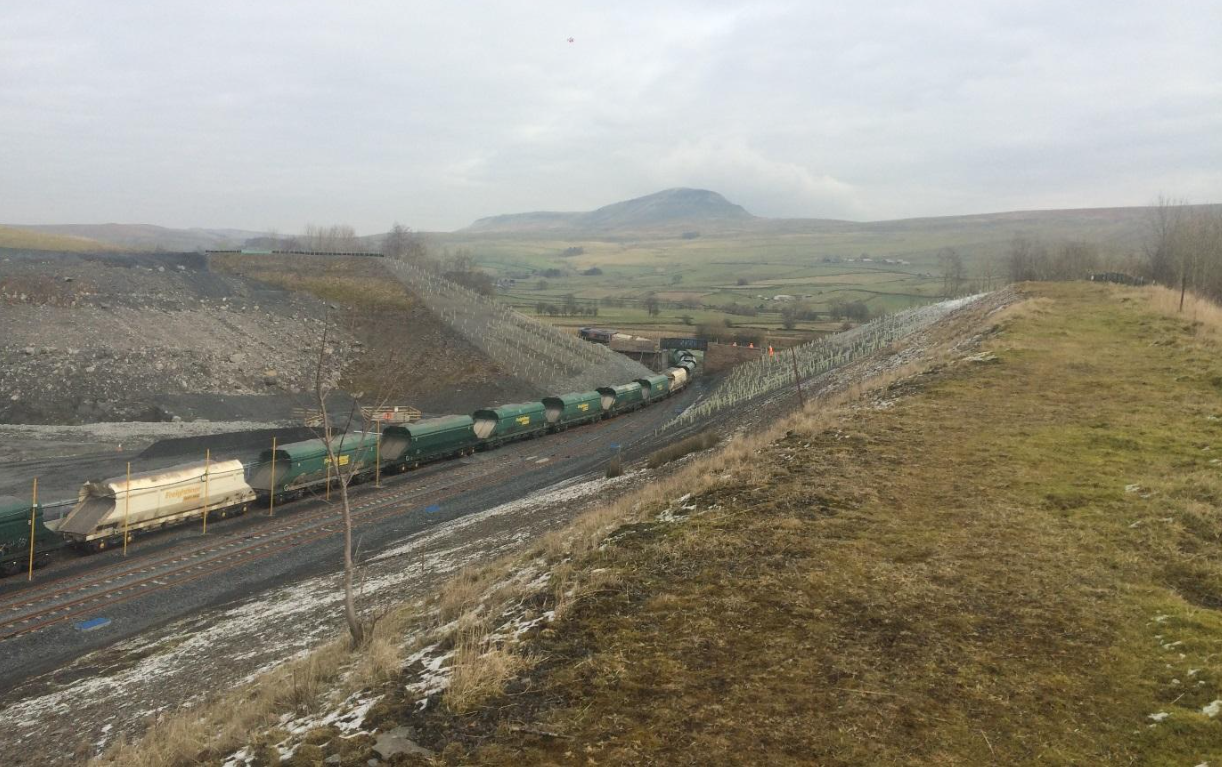
Understanding The Importance Of Dust Suppression Systems For Wagon Freight
Transporting dry bulk materials by rail can cause high volumes of dust to be blown up from open top wagons. This can trigger a range of environmental, health, and safety risks. Coal dust, for instance, can contaminate soil and water resources alongside rail routes and wagon freight, while silica dust from construction products contributes to fine particle pollution which may increase the rates of asthma, heart disease, and other respiratory issues for people living and working near transit routes.

When and Where To Implement A Dust Suppression System
To avert these risks, it is important for operators to effectively control dust emissions from rail wagons. However, where and when is the best place to strategically implement your dust suppression procedures?
The places to target first are the areas that produce the most fugitive dust, and the areas at most risk of harm. In terms of production, the most dust-heavy parts of any rail logistics process are the loading and unloading bays, while the most environmentally and health-sensitive parts of the chain are wagon freight adjoining farmland, designated natural areas, and housing.
Dust control systems are especially important for wagon freights used to transmit materials through sensitive areas, such as residential areas, passenger railway stations and park and drives, and parkland, especially if those materials contain known health hazards – such as silica.
What Are Your Road Dust Suppression Options?
There are four main dust suppression systems used for environmental management and control. These are:
-
-
-
-
-
-
-
-
-
-
-
-
Polymer-based Coatings: these dust suppression systems create a firm top layer or veneer on top of powdered materials that remains intact during transit. This minimises product loss and reduces the risk of dust -related health problems for employees and the general public. However, these coatings can be expensive and time-consuming to apply and remove.
-
-
-
-
-
Dust Suppression Sealants: Applying sealant to your load is a more cost-effective solution. These use a spray manifold to create a spray curtain over high-risk dust escape routes during unloading, significantly reducing your dust emissions. The substance applied is usually pressurised water mixed with binders, humectants, and surfactants to prevent the dust from becoming airborne and spreading.
-
-
-
Water Misting Systems: many operators use water misting systems to suppress dust in rail loading and unloading bays. This can be effective at controlling the problem of airborne dust and reduces dependence on chemical treatments, but isn’t suitable for all products.
-
Foam Dust Suppression: Foam dust suppression systems use a mixture of compressed air with water and foaming agents to create a foam that encapsulates the dust particles. The foam creates a blanket over the dust, which weighs it down and stops it from becoming airborne. The benefit of this system is that it uses minimal moisture, making it ideal for environments where excess water is problematic, and also for moisture sensitive products such as coal and cement. The binding agents in the solution provide long lasting and cost-effective dust control. When deployed at rail loading/unloading bays, foam systems can eliminate 90% or more of dust with minimal moisture, and require very little maintenance.
-
-
-
-
-
Find Out More
Please get in touch with the team at Best Chem today for more information about our road dust suppression systems for rail wagon encapsulation and how we can help.